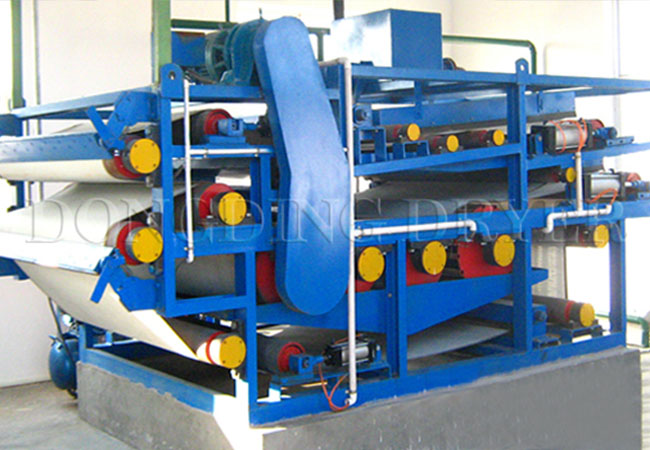
DYLT series belt filter press (belt dewatering machine) is a special dewatering equipment developed by our company for high-humidity muddy and bad residue materials. It successfully draws on advanced technology of domestic and foreign filter presses to produce a new type of dewatering equipment. , It is especially suitable for the dehydration of muddy materials and high-humidity bad residue materials. With continuous production, excellent dewatering effect, low power consumption, low noise, easy operation and maintenance, etc., its dehydration effect ranks first in China. On the basis of the original double mesh filter press, it has absorbed the latest principles and technologies of the latest concentration and pressure filtration dehydration at the end of the 1990s. It has developed and developed a new generation of integrated pressure filtration and dewatering integrated equipment. With continuous production, continuous cleaning, large processing capacity, low power consumption, low noise, convenient operation and maintenance, etc.
Working Principle
The fine wet slag raw materials enter into the hopper constantly through screw pump or conveyor(the material belt width is adjustable). Firstly, materials pass through an independent concentrating section where most free water is filtered, thus reducing the sludge slag liquidity. Then materials go through two annular filter belts. Under the driving of the driving roller, materials are distributed evenly by the spiral material press roller. They begin to enter into the curved arc wedge area for initial pressing and de-watering. Next, they enter into low pressure area where the compression roller with a L type mound layer extrudes large amount of water, and makes sure that water is discharged from both sides. Then they enter into the butt clamping and extruding high pressure area, internal and external filter belts bypass several groups of butt clamping and extruding rollers of which the diameter is diminishing. Large amount of water is strongly extruded slowly, forming compressible filter cake. On the other hand, the filter belt twines in S shape, and produces increasing surface pressure and shear force. Under the filter belt tension effect, the pressure produced by outer layer filter belt squeezes a small amount of water in the water out. As the press roller diameter decreases gradually, the material pressure between the filter belt increases gradually, a small amount of water is discharged constantly. Large amount of water is discharged by strong clamp roller squeezing and pressing, then collected and discharged by the sink. After the inner and outer filter belts are separated, wear-resisting scraper device the scrapes the filter cake( pomace) on the working surface of the inner and outer filter belt after de-watering. In the end, high pressure solid cone convex shape cleaning nozzle forms fan crossing water belt, and washes mesh belt continuously, thus keeping constant de-watering effect.
Working Flow Chart
Belt roller pressure dehydration machine technical parameters
model |
bandwidth |
monitor rate (kw) |
Punching net water pressure (Mpa) |
Compressed air |
Dimensions
L×W×H(mm) |
Feed moisture content % |
Water content % |
Feed processing capacityT/D |
Air consumption (m3/min) |
pressure(bar) |
DYLT1000 |
1000 |
2.2 |
≥0.5 |
0.2 |
4.0 |
5180×1640×2280 |
76~82 |
50~65 |
30~40 |
DYLT1500 |
1500 |
3.0 |
≥0.5 |
0.3 |
4.0 |
5180×2240×2280 |
76~82 |
50~65 |
40~45 |
DYLT2000 |
2000 |
4.0 |
≥0.5 |
0.3 |
4.0 |
5180×2640×2280 |
76~82 |
50~65 |
55~75 |
DYLT2500 |
2500 |
5.5 |
≥0.5 |
0.3 |
4.0 |
5180×3140×2280 |
76~82 |
50~65 |
75~100 |
DYLT3000 |
3000 |
7.5 |
≥0.5 |
0.3 |
4.0 |
5180×3640×2280 |
76~82 |
50~65 |
95~120 |
With continuous production, continuous cleaning, large processing capacity, low power consumption, low noise, easy operation and maintenance, etc.
model |
bandwidth |
monitor rate (kw) |
Punching net water pressure (Mpa) |
Compressed air |
Dimensions
L×W×H(mm) |
Feed moisture content % |
Water content % |
Feed processing capacityT/D |
Air consumption (m3/min) |
pressure(bar) |
DYLT1000 |
1000 |
2.2 |
≥0.5 |
0.2 |
4.0 |
5180×1640×2280 |
76~82 |
50~65 |
30~40 |
DYLT1500 |
1500 |
3.0 |
≥0.5 |
0.3 |
4.0 |
5180×2240×2280 |
76~82 |
50~65 |
40~45 |
DYLT2000 |
2000 |
4.0 |
≥0.5 |
0.3 |
4.0 |
5180×2640×2280 |
76~82 |
50~65 |
55~75 |
DYLT2500 |
2500 |
5.5 |
≥0.5 |
0.3 |
4.0 |
5180×3140×2280 |
76~82 |
50~65 |
75~100 |
DYLT3000 |
3000 |
7.5 |
≥0.5 |
0.3 |
4.0 |
5180×3640×2280 |
76~82 |
50~65 |
95~120 |